Before Jon Burmeister arrived at Skyline, no one had ever held his job. Technicians would look in the warehouse to grab materials, but there was no real method of organization. This was okay for a small business without many jobs or materials but with the growth that Skyline has experienced it became clear that change was needed.
Jon took charge of both organizing the warehouse at Skyline’s former building and of creating a system of organization to be used in the new warehouse. The first thing he did to initiate these changes in the old warehouse was create a walkway in the disorganized warehouse so that he could take a step back and get a good look at what was in it. He assessed the materials and began to organize them in his head. One challenge he encountered was that many of the materials that Skyline works with were new to him. But, with a bit of help from others at Skyline, he quickly learned about all the products and the scopes of work they belong to.
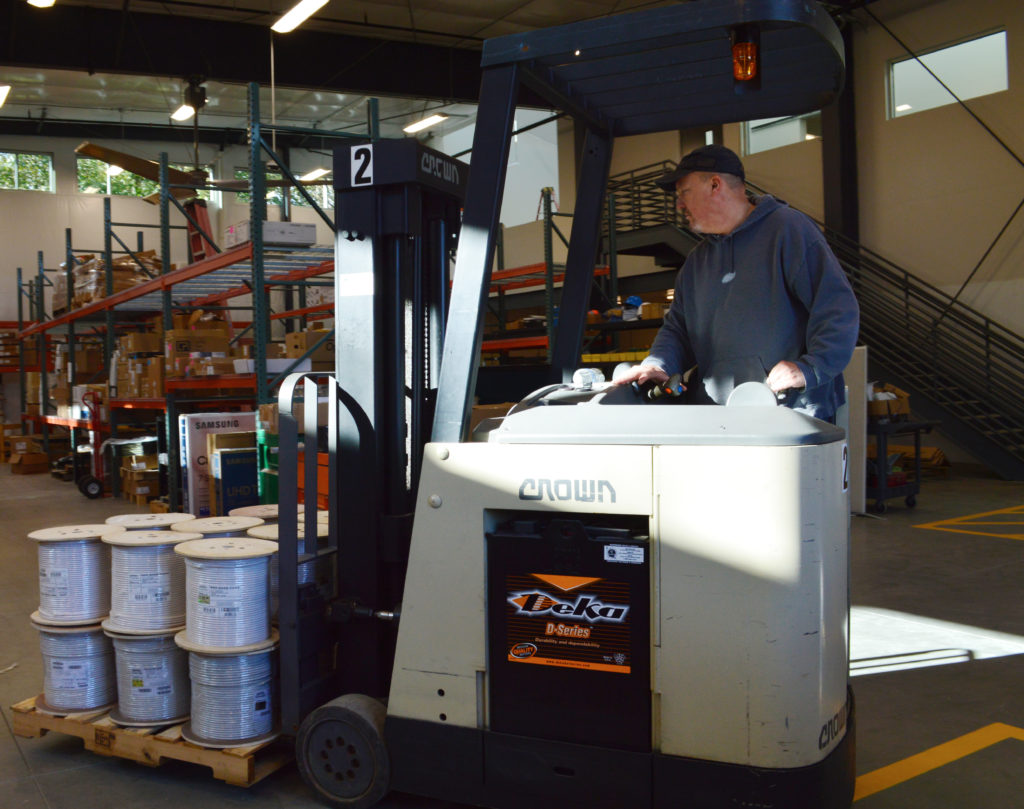
Using this knowledge, Jon was able to create a locater system in the new warehouse. No longer would anyone need to walk around searching for something, now it is easy to walk right up to whatever materials are needed. The warehouse is laid out with three large racks and in three divisions- DAS, service, and projects. Every day, Jon purchases products, receives products, labels products, and places products in their designated location. He also researches order statuses for materials needed. Sometimes product delivery times don’t match expectations, so Jon works with others at Skyline to stay ahead, meet deadlines, and please customers. Purchasing all the necessary materials and managing the entire warehouse are both big jobs, but Jon makes these jobs complement each other. When he purchases material, he mentally visualizes where the materials will need to go as they arrive, which allows him to stay organized and ahead-of-the-game.